Bioplastics: definition, manufacture and applications
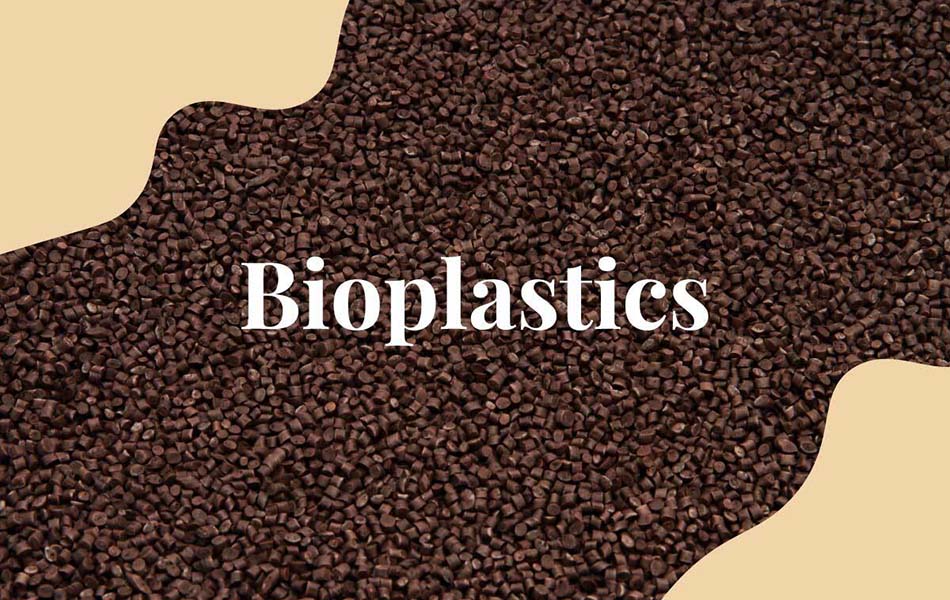
The term “bioplastic”, or “biopolymer” brings together two categories of materials:
- Bio-based plastics: they are synthetized from biomass, a renewable resource, and are opposed to fossil-based plastics.
- Biodegradable plastics: these are polymers that can be easily decomposed by microorganisms (bacteria, fungi, algae, etc.), when placed in a favorable environment (temperature, oxygen conditions, etc.).
Thus, we distinguish three possible combinations of bioplastic, or biopolymer, categories:
- Exclusively bio-based biopolymers : Bio-PE, Bio-PP, Bio-PVC, Bio-PET…
- Exclusively biodegradable biopolymers : PBAT, PCL, etc.
- Bio-based and biodegradable biopolymers PLA, PHA, etc.
Some bioplastic products available for consumption can be identified by the presence of specific labels, such as the EU compostability one.
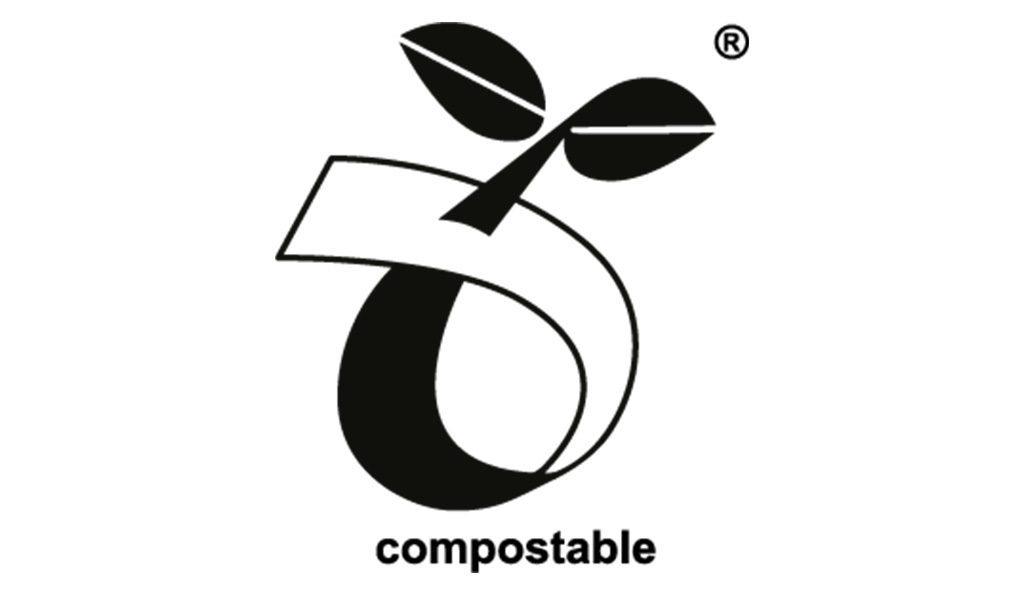
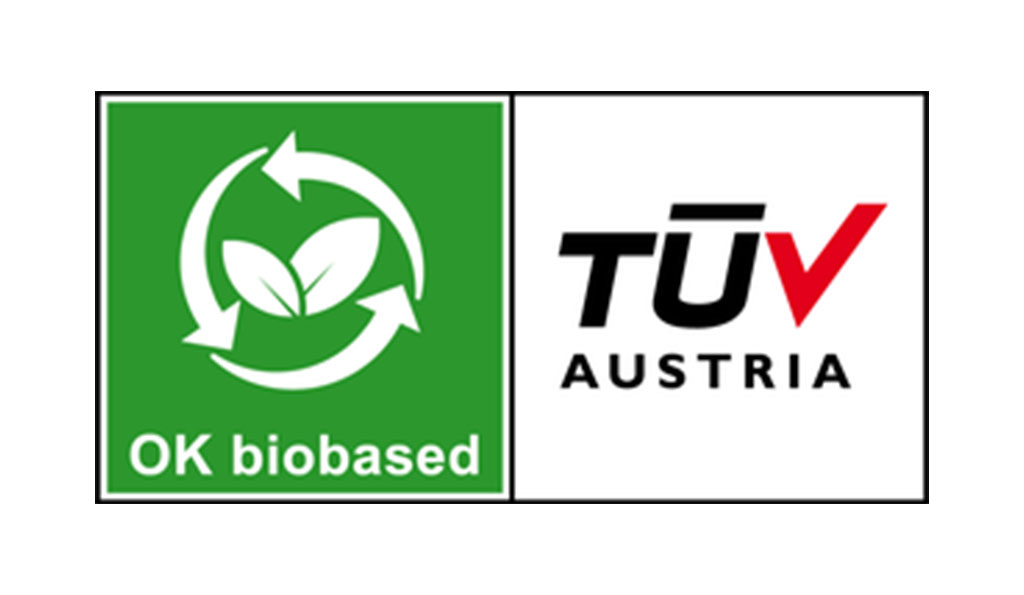
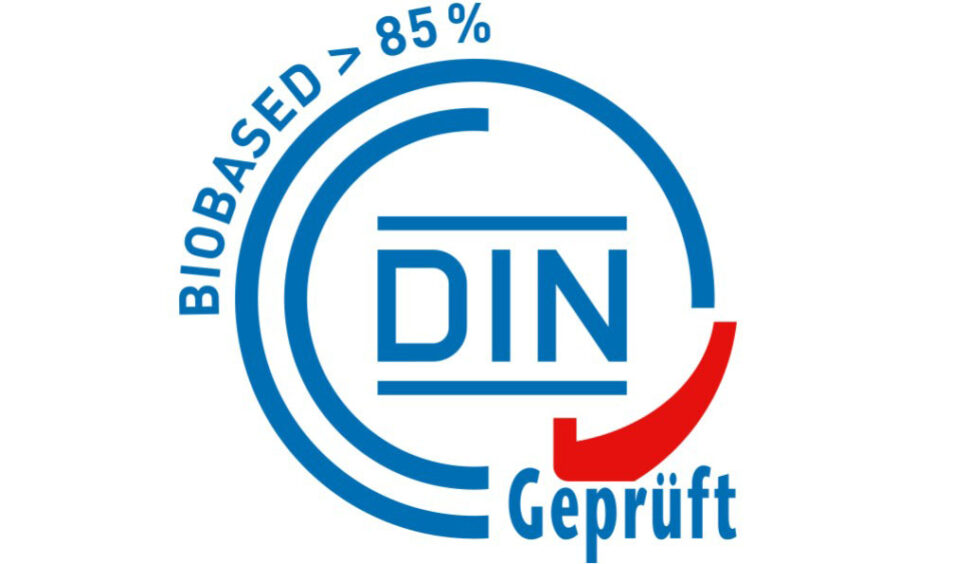
Compostability is also an indicator of biodegradability. Indeed, compostable plastic is necessarily biodegradable. However, the opposite is not always true.
Today, only 1% of the world’s plastic is bioplastic. A smaller proportion of this bioplastic is bio-based and biodegradable, and as such part of the third category above mentioned.
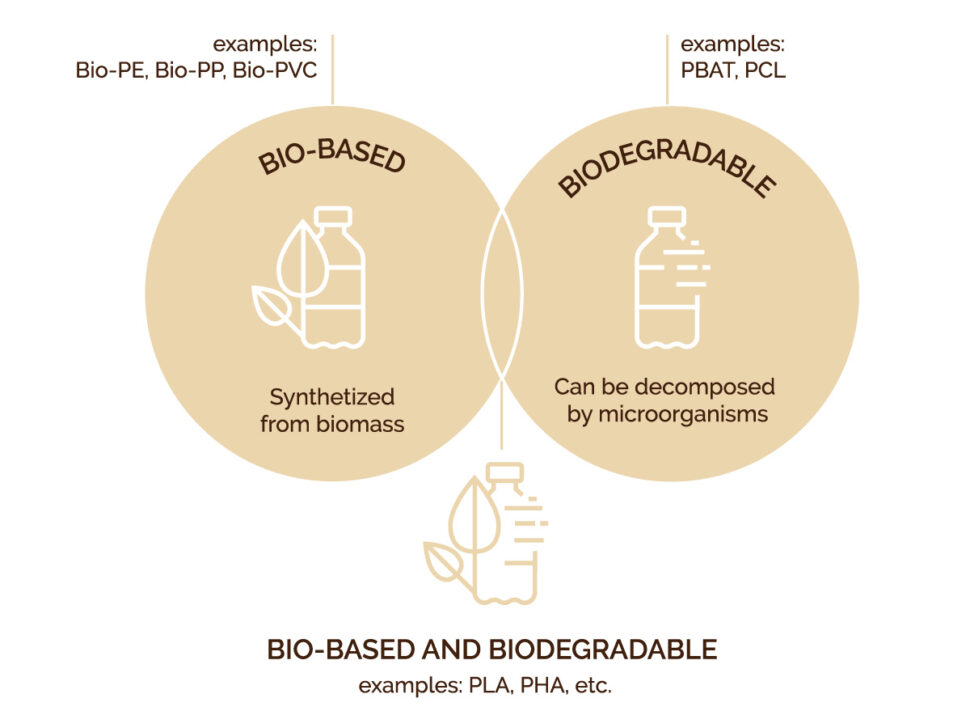
Table of Contents
The manufacture of biopolymers
The production of bioplastics from raw materials integrates several key techniques:
- Fermentation: sugars from biomass such as corn or sugarcane are fermented to produce polymers like polylactic acid (PLA).
- Polymerization: bio-based monomers (e.g., bio-ethylene) are chemically linked into long chains to form polymers akin to traditional plastics like polyethylene.
- Synthetic biology: microorganisms are engineered to synthesize complex biopolymers directly from agricultural byproducts, producing materials like PHA.
- Extraction and purification: These steps ensure the bioplastic is free from impurities and suitable for further processing, making it ready for industrial use in various forms.
Bioplastics are typically sold in granule form. The following are the main production processes in which they are used.
- Thermoforming and injection molding: used to create rigid products, these processes involve heating bioplastics to form specific shapes. Thermoforming heats sheets of plastic to mold them, while injection molding injects molten bioplastic into molds.
- Extrusion: a process where bioplastic granules are melted and forced through a die to create long continuous shapes like pipes, rods, and profiles. The material is then cooled to retain its shape.
- Film casting: involves extruding the melted bioplastic through a flat die followed by rapid cooling to produce thin films. These films are often used for packaging materials.
- Blow molding: this technique is used to achieve products with intermediate rigidity, such as bottles and containers, by inflating hot plastic in a mold.
3D printing: utilize a method called fused deposition modeling (FDM). This involves feeding bioplastic filament through a heated nozzle that melts the material. The printer then deposits the molten bioplastic layer by layer to build a three-dimensional object based on digital designs, allowing for complex geometries and custom designs.
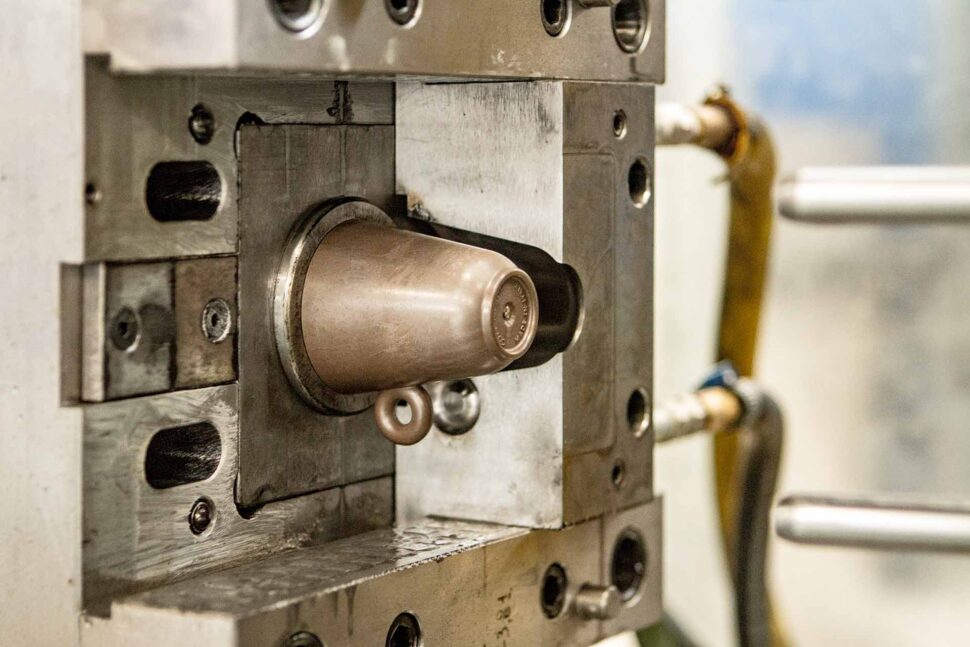
Expanding applications of bioplastics across key industries
Bioplastics are seeing diverse applications across various sectors, reflecting their growing importance in sustainable material solutions.
- In the packaging industry, bioplastics are increasingly used for food containers, bottles, and films, offering an eco-friendlier alternative to traditional plastics.
- The automotive sector is also integrating bioplastics, utilizing them in car interiors for components like dashboards and door panels to reduce environmental impact.
- Additionally, agriculture has adopted bioplastics for biodegradable mulch films, aiding in soil health management while minimizing waste.
- In consumer electronics, companies are exploring bioplastics for casings and accessories, aligning with corporate sustainability goals.
Each use case underlines the broad potential of bioplastics to contribute to greener manufacturing practices across industries.
Starch and cellulose: the oil of the 21st century
Thermoplastic starch (TPS), accounting for around 80% of the bioplastics market, is primarily derived from plants like maize, wheat, potatoes, and tapioca, and is the most commonly used bioplastic. It becomes malleable at certain temperatures, allowing it to be transformed into various objects. It is, along with cellulose extracted from wood or plant waste, favored for its ability to be shaped within a specific temperature range.
Polylactic acid (PLA), another major bioplastic, is known for its versatility and low environmental impact. Sourced from fermented plant starch such as corn, sugarcane, or cassava, PLA is biodegradable, widely used in packaging, disposable tableware, and medical implants, and is actively being researched to enhance its thermal and mechanical properties. PLA is the most widely used in 3D printing due to its low softening and melting temperatureOur Coffeefrom® Bio material merges PLA with coffee, resulting in a 100% biodegradable product ideal for applications requiring a minimal ecological footprint.
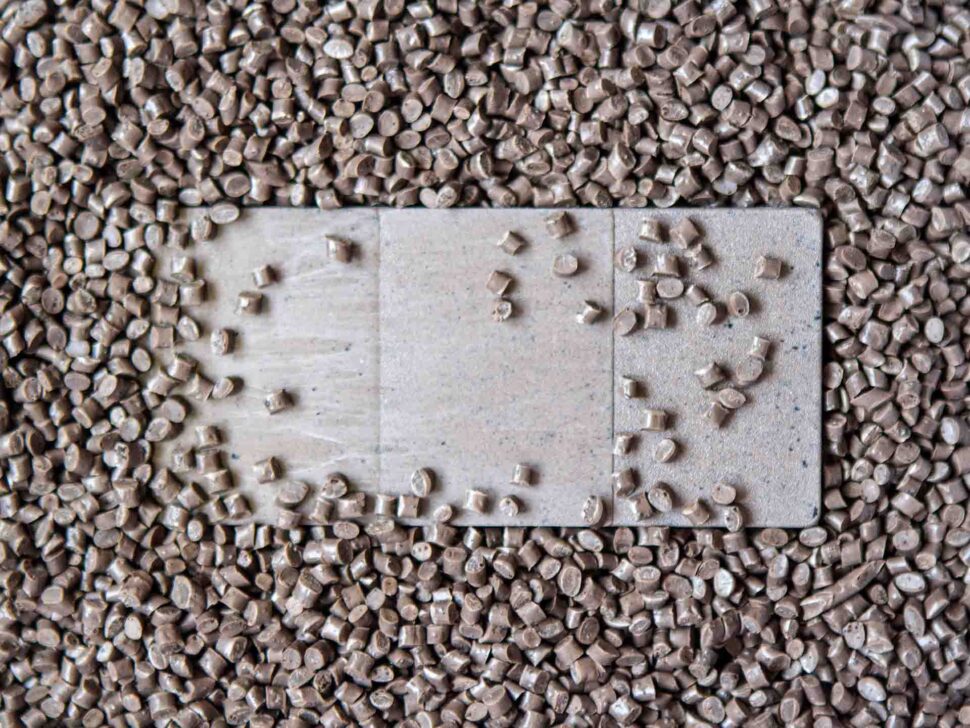
Innovating bioplastics: blending recycled polyethylene (PE) with used coffee grounds
Companies are adopting bioplastics to lessen the environmental impact of traditional plastics, as bioplastics, when burned, release CO2 equivalent to what their source plants absorb, and compostable types help reduce pollution. However, the cultivation of bioplastics’ raw materials, like maize and wheat, often requires significant water, fertilizer, and pesticides, which can harm the environment and also divert these crops from food supplies, complicating the environmental benefits of bioplastics.
On these premises, recycled polyethylene (PE) mixed with used coffee grounds leverages the high availability of PE waste and the organic properties of coffee grounds to create a composite that can be used for the most diverse applications.
Coffee grounds, a byproduct of coffee consumption, offer a value-added proposition by reducing waste that would otherwise end up in landfills. The process of integrating these grounds with recycled PE aligns with circular economy principles, turning waste into a resource and thus minimizing the environmental impact associated with plastic production.
Coffeefrom® Eco blends recycled LDPE (low-density polyethylene) with coffee grounds, creating a 100% recycled material that not only reduces waste but also gives new life to existing plastic materials.
Coffeefrom® Strong uses HDPE (high-density polyethylene) enriched with coffee grounds to provide a solution that combines high temperature resistance and food contact certification, making it particularly suitable for packaging in the food industry.
Conclusions
The journey through the world of bioplastics reveals a landscape rich with potential and fraught with challenges.
From packaging to automotive parts, bioplastics are slowly infiltrating various sectors, driven by the dual forces of innovation and necessity.
However, the road ahead is complex, with hurdles related to production efficiency, cost-effectiveness, and the environmental impact of raw material cultivation. As we continue to innovate and optimize the use of bioplastics, particularly with exciting developments like those using recycled PE and spent coffee grounds, it is crucial to balance ecological benefits with practical viability.
Finally, the evolution of bioplastics is not just about replacing traditional plastics but rethinking our material economy for a sustainable world.