Exploring bioplastic production methods and industrial applications
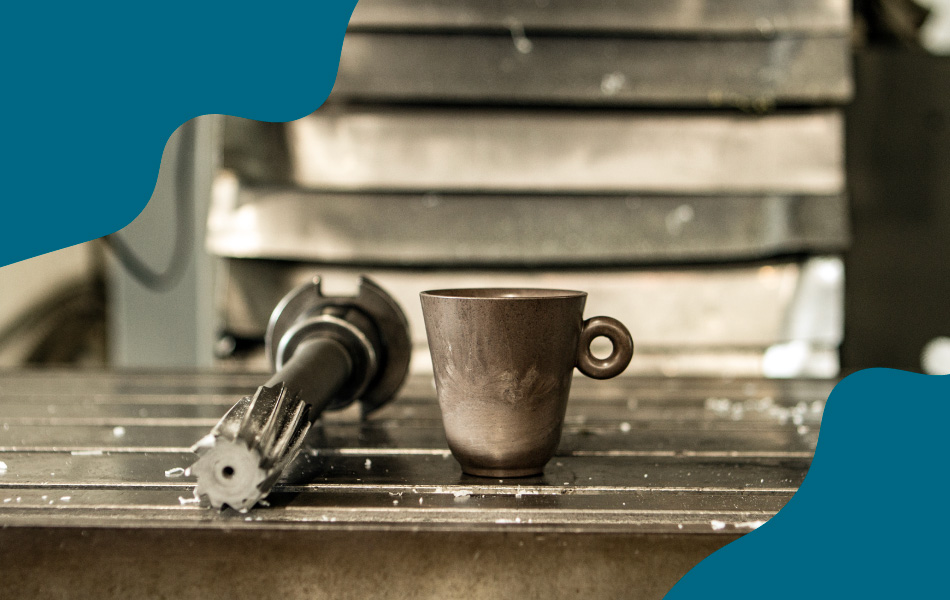
The global shift towards sustainability has catalyzed significant advancements in bioplastics and biopolymers. Derived from renewable resources, these materials usually offer a more eco-friendly alternative to conventional plastics. This article explores the production methods of bioplastics and biopolymers and delves into the industrial techniques used to create various products from these materials, including thermoforming, injection molding, extrusion, film casting, blow molding, and 3D printing. We’ll also introduce our innovative product, Coffeefrom® Bio, which exemplifies the potential of bioplastics in diverse applications.
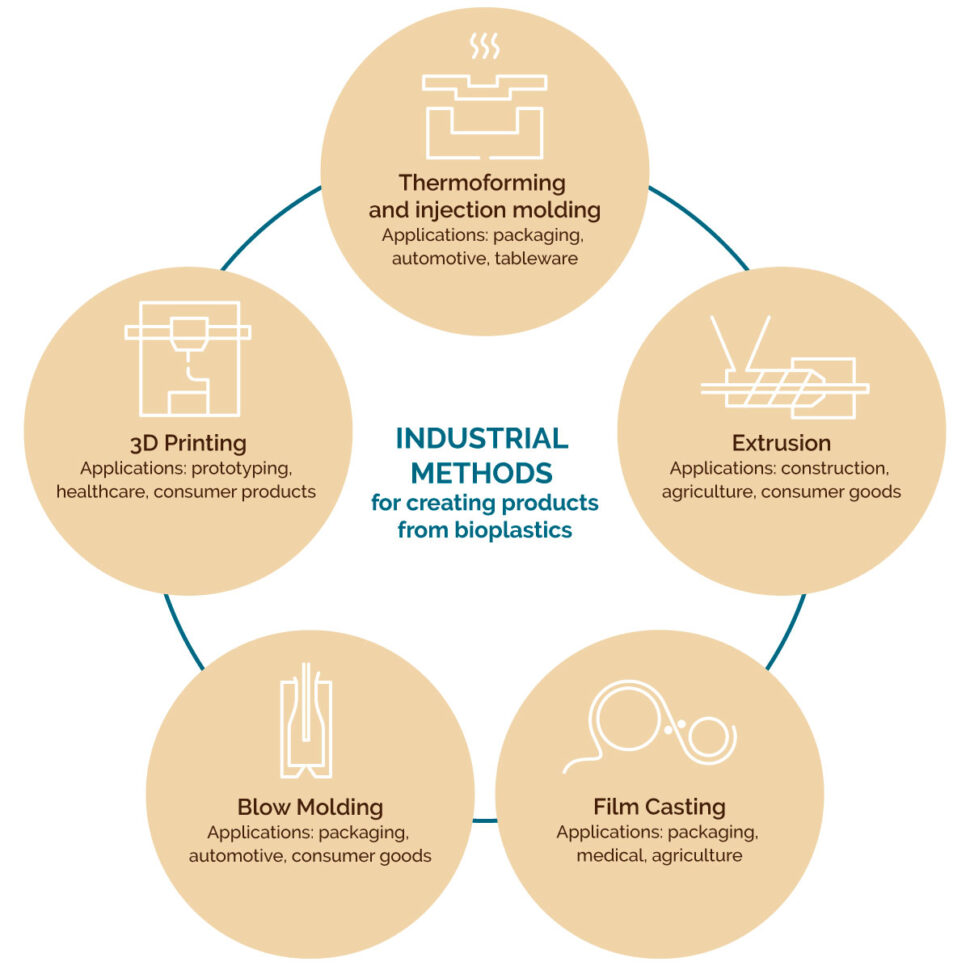
Table of Contents
Bioplastic and biopolymer production methods
Starch-based plastics
Starch-based plastics are one of the most common types of bioplastics, produced from corn, potato, or tapioca starch. The production process involves:
- Extraction: starch is extracted from the chosen crop.
- Gelatinization: the starch is mixed with plasticizers (like water and glycerol) and heated to form a gel-like substance.
- Polymerization: this gel is then processed to create a thermoplastic material.
Polylactic acid (PLA)
PLA is derived from fermented plant sugars, typically from corn starch or sugarcane. The production steps include:
- Fermentation: plant sugars are fermented to produce lactic acid.
- Polycondensation: lactic acid molecules are linked together to form PLA through a condensation reaction.
- Purification: the PLA is then purified and pelletized for use in various industrial processes.
Polyhydroxyalkanoates (PHA)
PHA is produced by bacterial fermentation of sugars or lipids. The production process involves:
- Fermentation: specific bacteria are cultivated in a nutrient-rich environment to produce PHA granules inside their cells.
- Extraction: PHA is extracted from the bacterial cells and purified.
- Processing: the purified PHA is then processed into pellets for industrial applications.
Cellulose-based plastics
Cellulose-based plastics are made from cellulose, a natural polymer found in plant cell walls. The production involves:
- Dissolution: cellulose is dissolved in a suitable solvent.
- Regeneration: the dissolved cellulose is regenerated into fibers or films through a process of precipitation or coagulation.
- Modification: the cellulose can be chemically modified to improve its properties for specific applications.
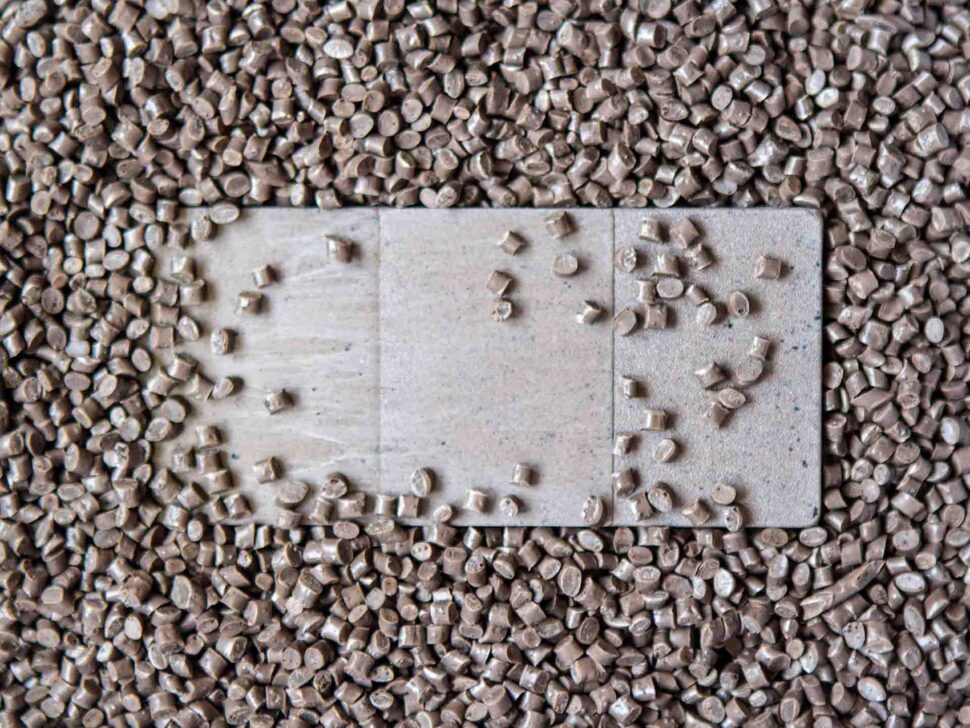
Introducing Coffeefrom® Bio
Coffeefrom® Bio is our groundbreaking material, consisting of coffee grounds of industrial origin (10-20% in variable composition) mixed with the biopolymer PLA. This innovative bioplastic was developed through scientific research in collaboration with the Department of Chemistry “Giulio Natta” of the Politecnico di Milano and Fondazione Politecnico di Milano.
Key features of Coffeefrom® Bio:
- Renewable and organic: made from coffee grounds and PLA, Coffeefrom® Bio is derived from renewable resources.
- Biodegradable: the material is 100% biodegradable, ensuring it breaks down naturally without harming the environment.
- Versatile applications: suitable for injection molding and 3D printing, Coffeefrom® Bio can be used in multiple application fields, including packaging, automotive, tableware, and service products.
Industrial methods for creating products from bioplastics
We will now dwell on the industrial processes that are used to create marketable goods from bioplastic.
Thermoforming and injection molding
These processes are used to create rigid products by heating bioplastics to form specific shapes.
- Thermoforming: involves heating sheets of bioplastic and molding them into desired shapes.
- Injection Molding: involves injecting molten bioplastic into molds to form complex and precise parts.
Applications:
- Packaging: clamshell containers, trays, and lids.
- Automotive: interior panels, dashboards, and trim components.
- Tableware: plates, bowls, and cutlery.
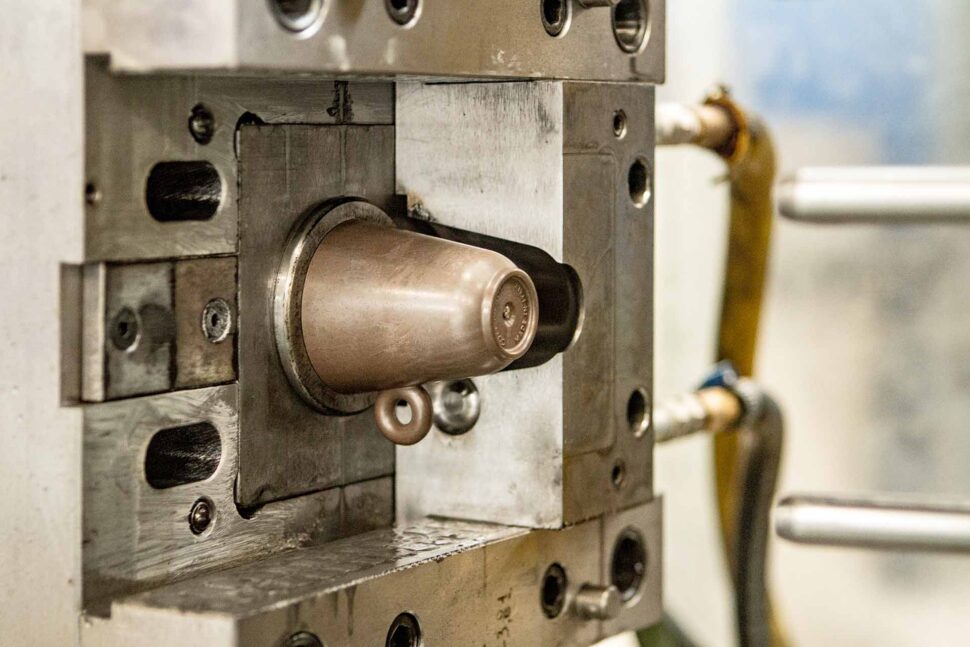
Extrusion
Extrusion involves melting bioplastic granules and forcing them through a die to create long continuous shapes like pipes, rods, and profiles. The material is then cooled to retain its shape.
Applications:
- Construction: pipes, tubing, and profiles for window frames.
- Agriculture: drip irrigation tubing and greenhouse structures.
- Consumer Goods: curtain rods, and decorative trims.
Film casting
Film casting involves extruding melted bioplastic through a flat die followed by rapid cooling to produce thin films.
Applications:
- Packaging: food wraps, bags, and shrink films.
- Medical: sterile packaging and disposable gloves.
- Agriculture: mulch films and silage wraps.
Blow molding
This technique is used to achieve products with intermediate rigidity by inflating hot bioplastic in a mold.
Applications:
- Packaging: bottles for beverages, cosmetics, and household cleaners.
- Automotive: fuel tanks and air ducts.
- Consumer Goods: containers for detergents and toiletries.
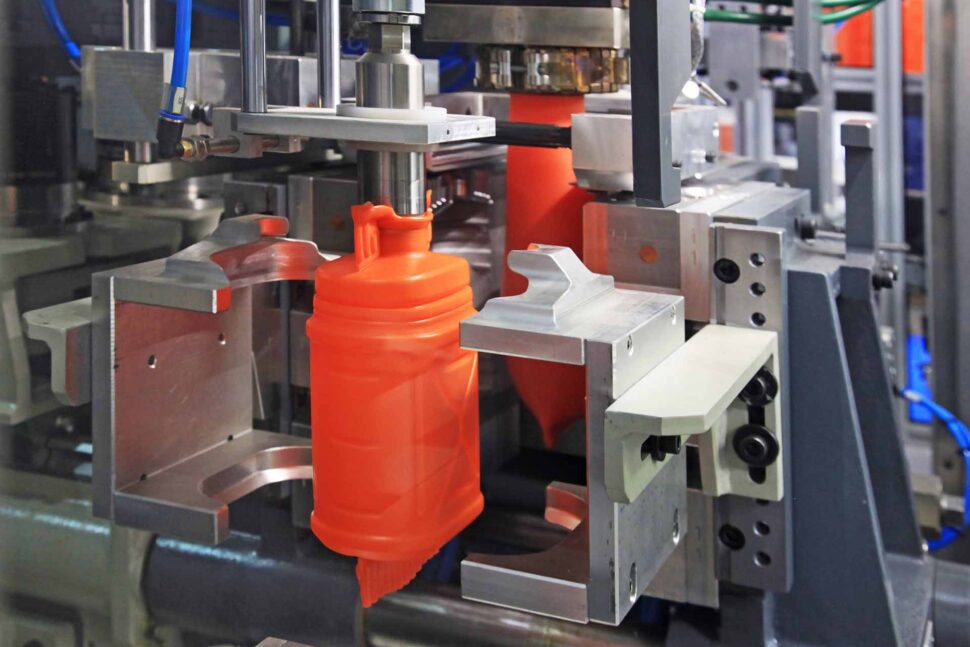
3D Printing
3D printing utilizes a method called fused deposition modeling (FDM), which involves feeding bioplastic filament through a heated nozzle that melts the material. The printer then deposits the molten bioplastic layer by layer to build a three-dimensional object based on digital designs, allowing for complex geometries and custom designs.
Applications:
- Prototyping: custom prototypes and design iterations.
- Healthcare: customized prosthetics and implants.
- Consumer products: personalized items like phone cases and jewelry. Coffeefrom® Bio is particularly suitable for these applications due to its unique composition and aesthetic appeal.
Future prospects and challenges
The future of bioplastics is promising, with continuous advancements in material properties and production techniques. Innovations are expanding the range of applications and making bioplastics more competitive with traditional plastics.
Despite the progress, bioplastics face challenges such as higher production costs, scalability issues, and the need for specialized recycling infrastructure. Overcoming these challenges will be crucial for the widespread adoption of bioplastics.
Conclusion
Bioplastics and biopolymers are pivotal for a sustainable future, offering eco-friendly alternatives to traditional plastics. This article explored key production methods like starch-based plastics, PLA, PHA, and cellulose-based plastics. It also highlighted industrial processes such as thermoforming, injection molding, extrusion, film casting, blow molding, and 3D printing. Our innovative Coffeefrom® Bio showcases the practical and aesthetic benefits of bioplastics.