HDPE vs. LDPE: recycling and reimagining our most common plastics
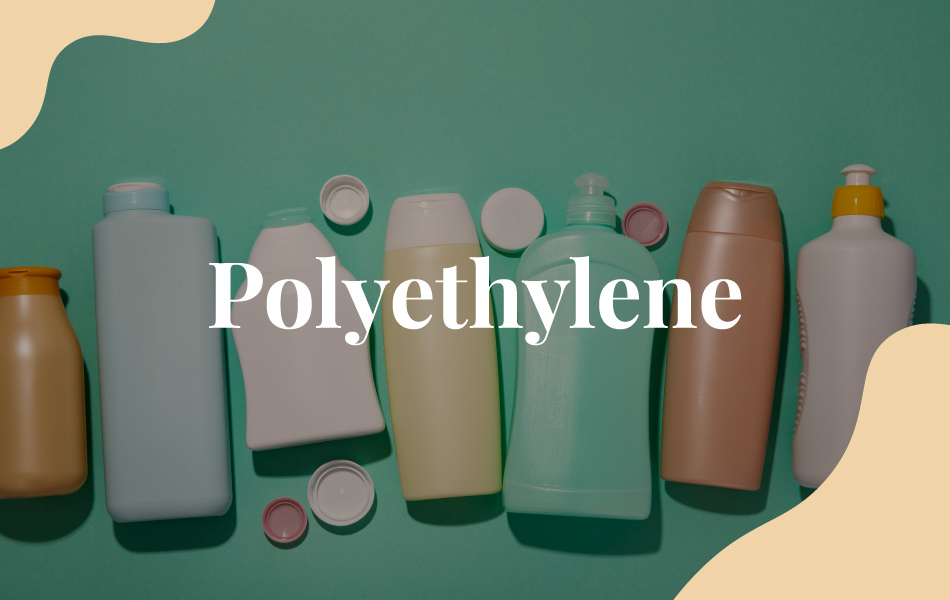
High-Density Polyethylene (HDPE) and Low-Density Polyethylene (LDPE) are two of the most common plastics used in everyday items. Recycling these materials plays a crucial role in reducing plastic waste and conserving resources. While traditionally HDPE and LDPE haven’t been directly produced from organic materials, a promising alternative is emerging: bio-based PE.
Bio-based PE is polyethylene derived from renewable resources like sugarcane or corn, offering similar properties but with a potentially lower carbon footprint. Additionally, companies like Coffefrom are pioneering the use of recycled plastics and bio-based fillers to create innovative alternatives.
Table of Contents
HDPE: The workhorse plastic
HDPE, identified by the recycling symbol “2,” is a strong and rigid plastic commonly found in milk jugs, detergent bottles, and plastic lumber. Its recycling process involves collection, sorting, washing, grinding, melting, and remolding into new products.
Recycling HDPE offers significant benefits, including reduced reliance on virgin plastic, a potential reduction in greenhouse gas emissions and in plastic pollution. However, challenges remain, such as the energy required for processing and limitations in recycling certain colored HDPE items.
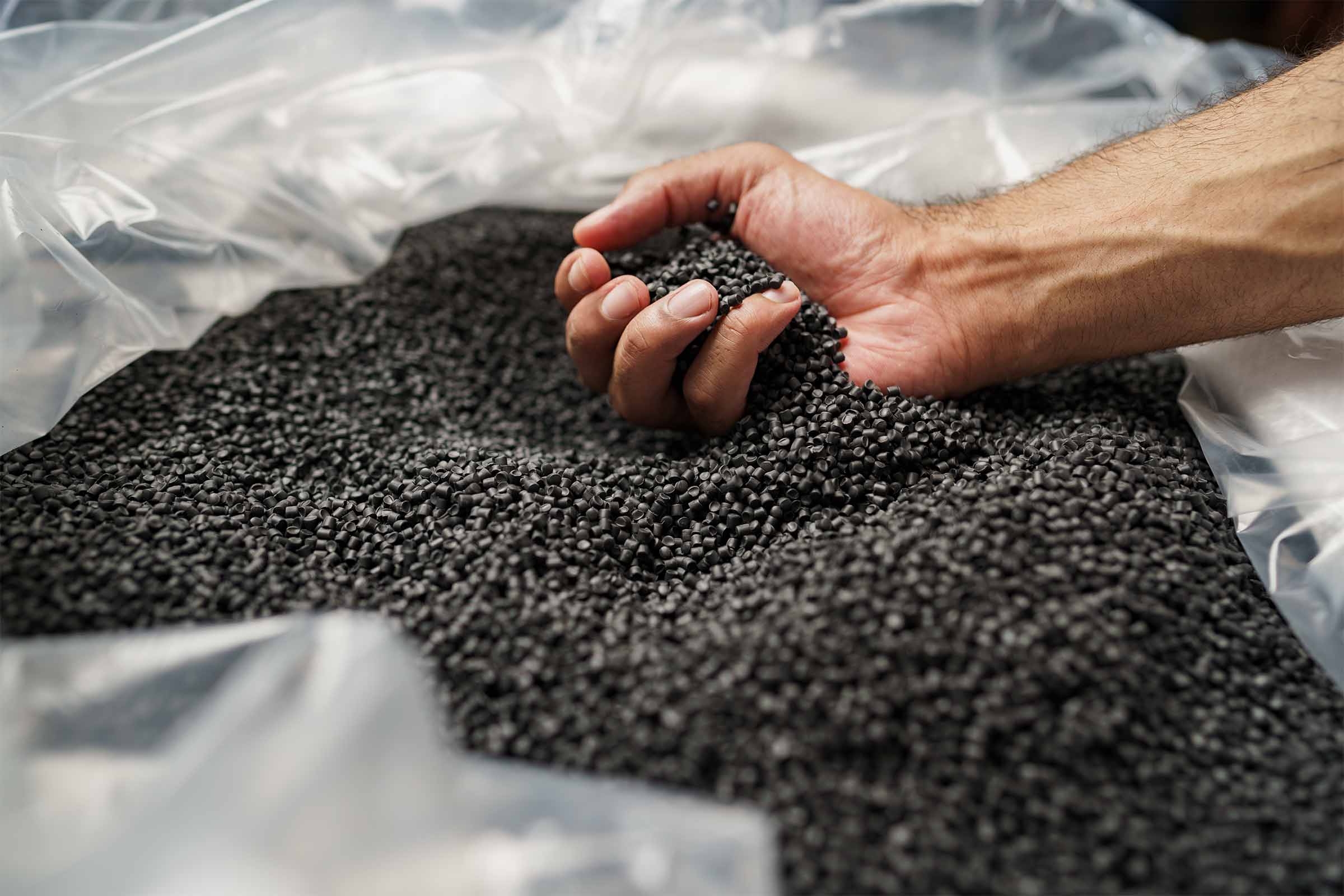
LDPE: the flexible choice
LDPE, with recycling symbol “4,” is known for its flexibility and is used in grocery bags, food wraps, and squeezable bottles. Its recycling process mirrors that of HDPE, but its lower melting point and tendency to cling to contaminants make it more complex.
Despite these hurdles, LDPE recycling offers advantages like reducing waste and creating valuable materials for new products. However, contamination and a lower market value compared to virgin LDPE remain obstacles.
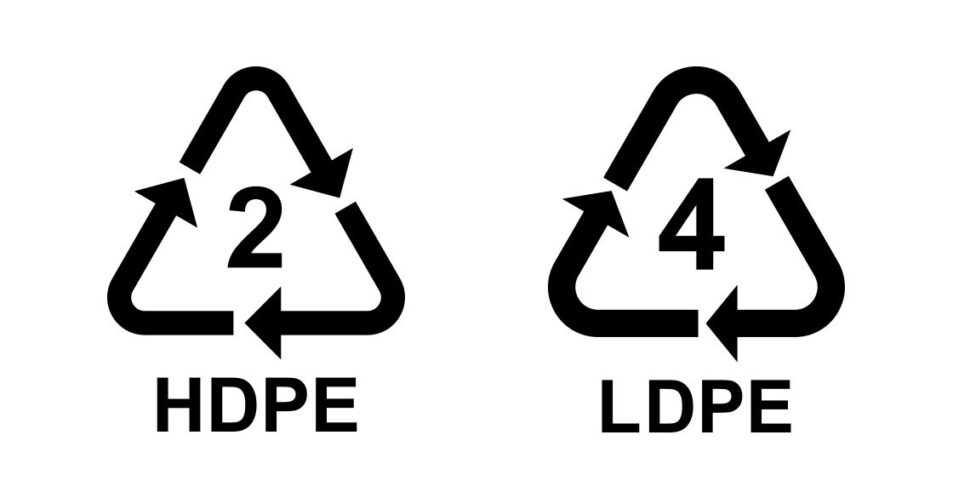
A tale of two plastics: HDPE vs. LDPE recycling
While both HDPE and LDPE are recycled, their processes and challenges differ. HDPE boasts a more established system with higher recycling rates, while LDPE recycling requires advancements to overcome contamination issues and improve economic viability.
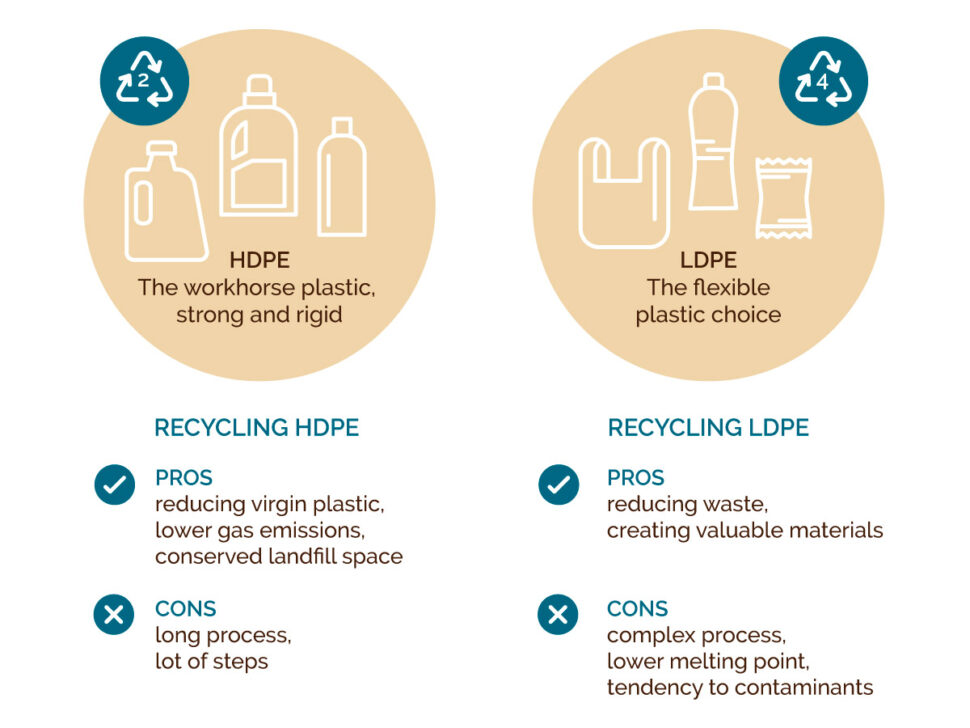
Rethinking polyethylene with spent coffee grounds
Exciting advancements are emerging in polyethylene usage and recycling.
Coffefrom® Eco, for instance, utilizes 10% coffee grounds blended with recycled LDPE, creating a unique and sustainable material for injection molding. This innovative approach demonstrates the potential for incorporating recycled plastics and bio-based fillers into the future of polyethylene products.
Coffefrom® Strong takes a similar approach, combining 10% coffee grounds with recycled HDPE to create a rigid material suitable for applications demanding higher mechanical properties.
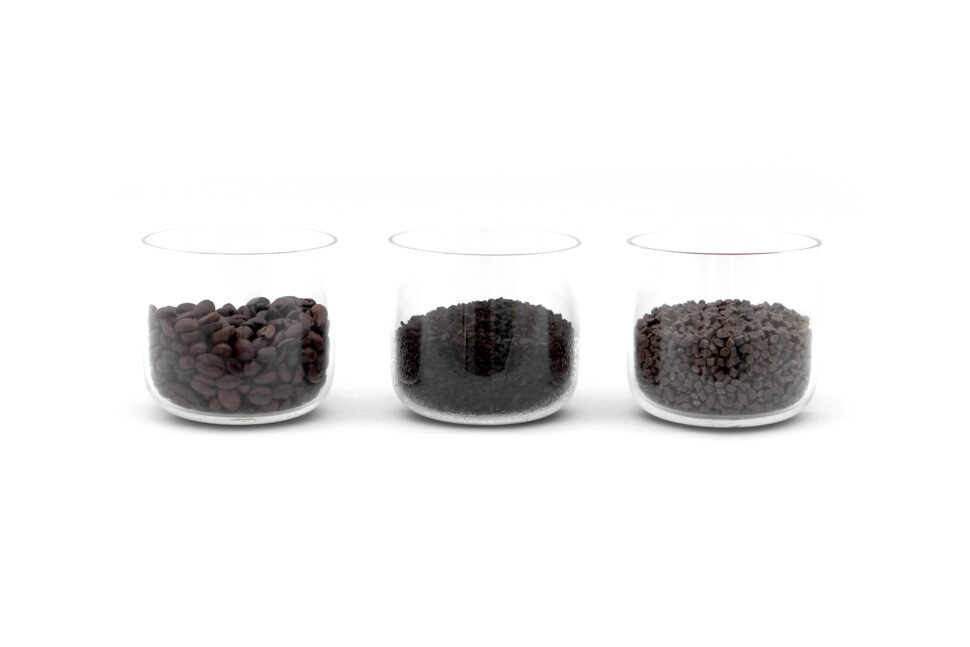
Conclusions
HDPE and LDPE are workhorse plastics, but responsible use is key. Recycling these materials reduces reliance on virgin plastic and conserves resources. Bio-based PE offers a promising future, while companies like Coffefrom are leading the way with innovative composites using recycled plastics and bio-based fillers.
These advancements, alongside continued recycling efforts, pave the way for a more circular future for polyethylene.